Built on Trust, Driven by Innovation.
At Cer Casting, we prioritize quality, trust, and customer satisfaction in everything we do. Our commitment to sustainability and innovation drives us to lead the industry with environmentally responsible practices and cutting-edge technology. With teamwork at our core, we confidently move forward, building on our legacy of excellence.
Quality & Trust
Customer Focus
Sustainability
Innovation
Teamwork
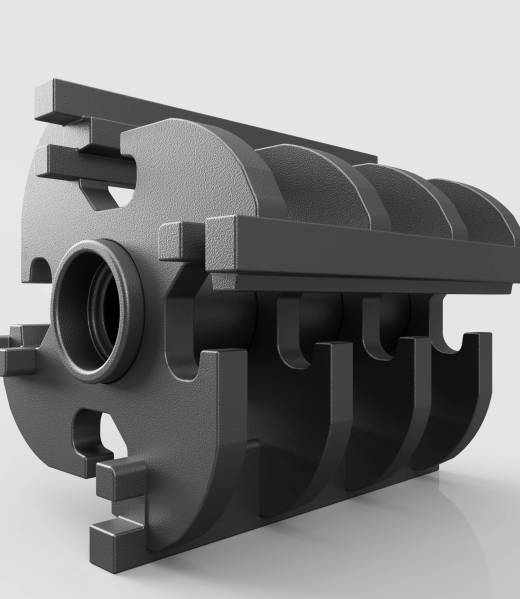
Our Production Process: Excellence in Every Pour
At Cer Casting, our production process combines precision, innovation, and expertise at every step. From selecting the optimal casting method to precise machining, we ensure that each component meets the highest standards for quality, durability, and performance.
Method
Our production begins with selecting the most efficient and accurate casting method based on customer requirements. Using simulation studies, we validate the design of the gating and feeding systems necessary for the part.
Pattern Shop
Based on the casting data from the customer, we begin model production. Depending on the quantity and specifications, we manufacture patterns using foam, wood, or aluminum. Our precise and efficient pattern production ensures a smooth transition to casting and machining stages.
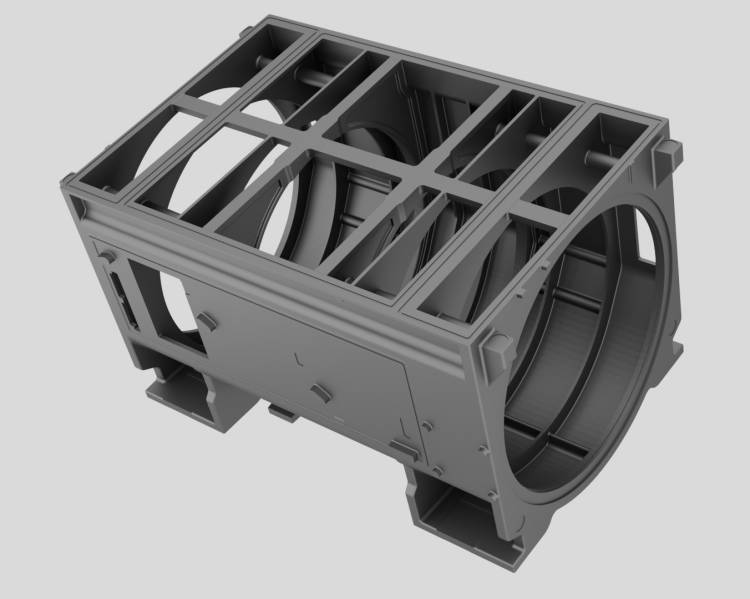
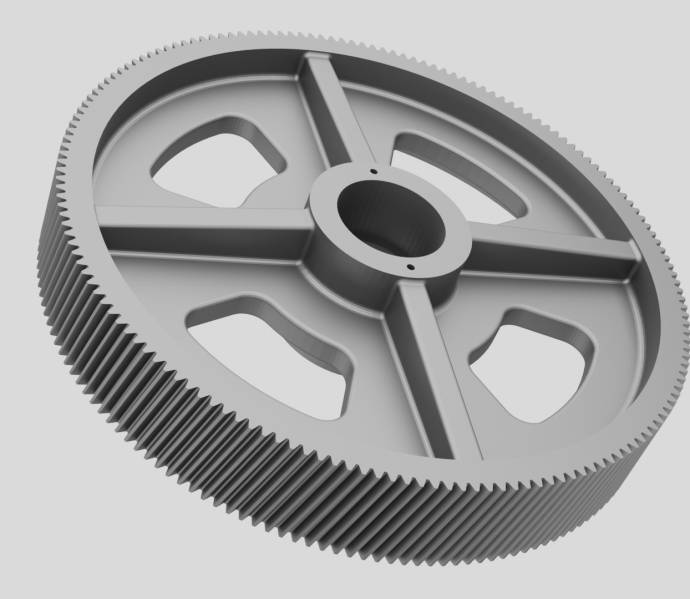
Molding
To achieve high-quality and efficient casting, we carefully prepare molds at the beginning of the process. We manage our molding operations with precision to maintain dimensional accuracy and surface quality. With two molding departments in our facility, we can produce molds for parts up to 20 tons using the Alphaset resin-bonded sand molding method with foam or wooden patterns, handled by our experienced team.
Melting
We conduct the melting process meticulously to meet the highest quality standards. Metals are melted in our furnaces, and once in liquid form, undergo strict temperature and chemical analysis checks before pouring to ensure readiness for the next production stage.
Cleaning & Grinding
We remove risers, runners, and gating systems from the cast parts and perform thorough surface cleaning. Heat treatments are applied to enhance the homogeneity and quality of the metal. Depending on customer requirements, we apply industrial painting techniques to enhance corrosion resistance and improve aesthetics.
Machining
As a crucial phase of the production process, we perform precision machining on high-accuracy parts in our CNC turning, boring, and vertical machining centers based on customer demands. Thanks to our modern machinery, we maintain exceptional dimensional precision and deliver top-quality products.
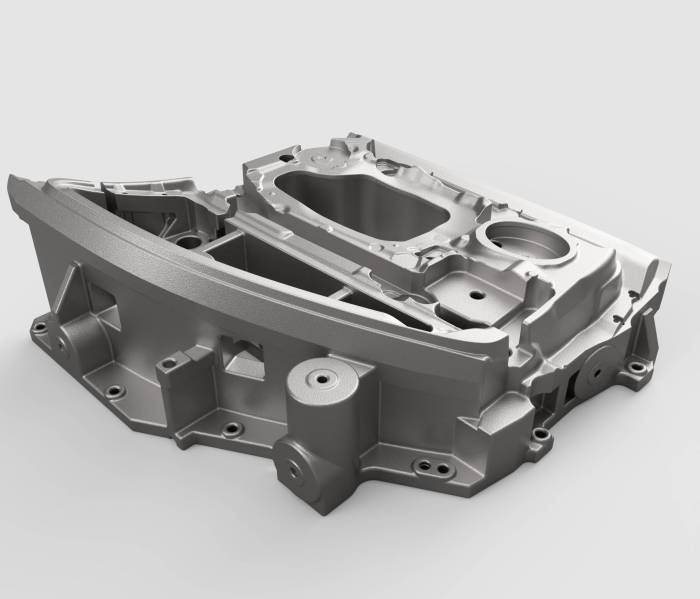
Cer Casting
Quality Control
We implement a rigorous quality control process at every stage of production to maintain the highest standards. We continuously improve our quality procedures and use advanced testing methods to ensure the best possible results.
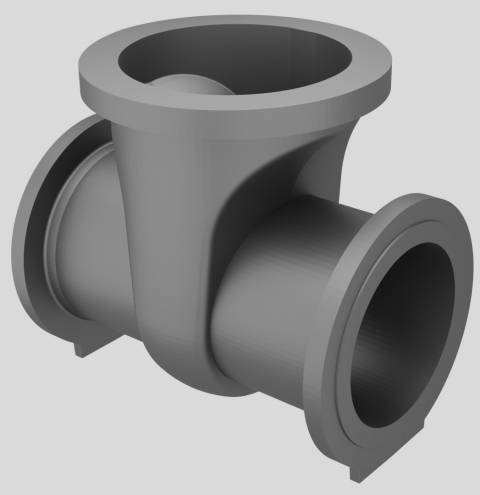
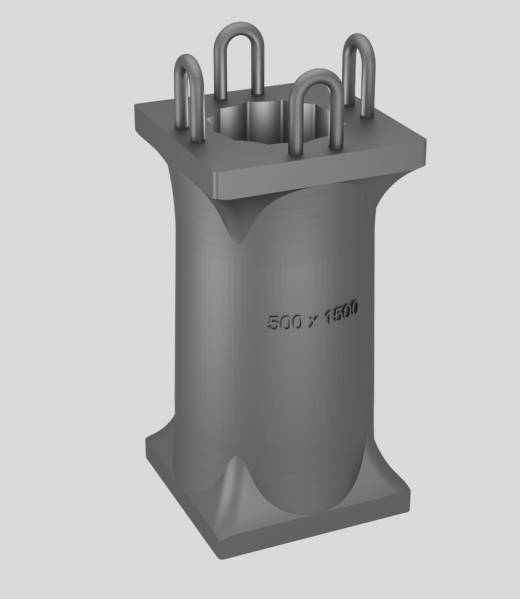
Incoming Inspection
All raw materials introduced into the production line are carefully examined to meet predefined quality standards. Only top-quality materials are used in production.
Process Control
Throughout the production process, in-process inspections are conducted to evaluate dimensional accuracy, surface finish, and mechanical properties. This helps detect and minimize potential defects early.
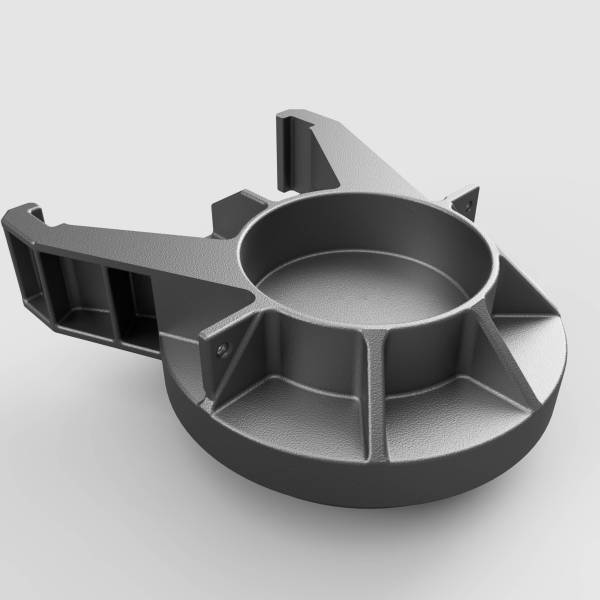
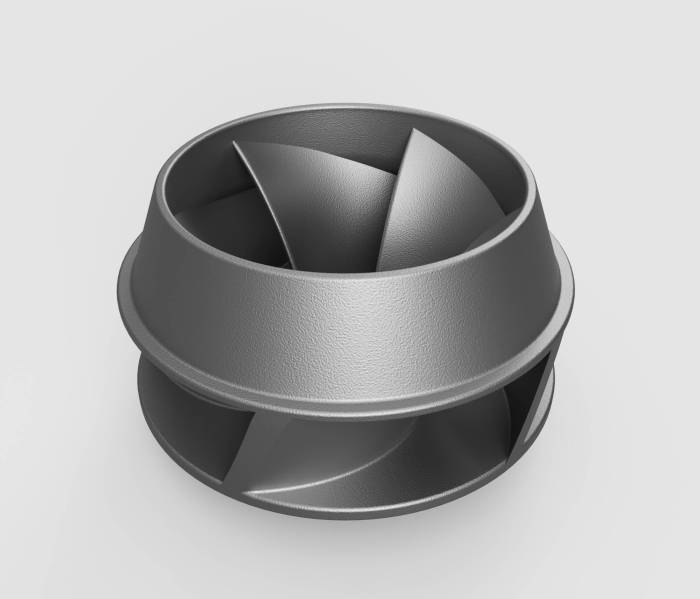
Final Inspection & Testing
Every part is tested thoroughly to verify compliance with customer requirements and international standards. Both destructive and non-destructive testing methods, along with precision measurement tools, are used to confirm product strength, durability, and functionality.
Certification & Reporting
All quality control processes are documented, and detailed reports are provided to our customers as proof of process reliability. When needed, we ensure compliance with national and international certification standards.
Our Quality Control Department, guided by the principle of “Quality First,” carefully monitors each stage of production, allowing us to deliver reliable, durable, and high-performance products to our customers.